The pressure sensing technology department of GE's inspection and control technology business has recently released a new trench etching resonance (TERPS) pressure sensor technology platform RPS8000, which can significantly increase the ability of the pressure test range related to traditional resonance pressure technology, while providing 10 times The accuracy and stability of the existing piezoresistive pressure sensor. Trench etching resonant pressure sensor is the result of in-depth research and development on the design and manufacturing process of existing silicon resonant pressure sensor. It is in the fields from aerospace to marine engineering, seabed exploration operations, from process technology to industrial instruments It is widely used. Manager Steve Sajben explained: By inheriting our Drucker technology, we have been able to provide RPT series of silicon resonance products a few years ago. During this time, we have further expanded and developed more advanced manufacturing processes through cooperation within the company and with relevant R & D institutions, so that the pressure sensors provided by GE not only have the inherent accuracy and stability of silicon resonance pressure sensors, And in terms of pressure range, temperature range and mechanical packaging have been greatly improved.
The working principle of the trench etching resonant (TERPS) pressure sensor is consistent with the existing resonant silicon pressure sensor of GE. The silicon resonance structure is driven by an electrostatic field. When pressure is applied to the diaphragm, the silicon resonator is stretched like a guitar string, changing its frequency. This frequency change is directly related to the applied pressure.
Because of the mechanical properties of the single crystal silicon structure, resonant silicon pressure sensors are more accurate and stable than piezoresistive and many other pressure measurement techniques. The main characteristic is that silicon is completely elastic before its breaking point. The perfect mechanical characteristics bring a high-quality resonance (high Q factor) to the sensor, and its frequency stability is not affected by the electronic characteristics of the product. In contrast, piezoresistive technology requires the introduction of resistive elements into the silicon crystal structure. The electrical performance of these stress sensitive resistors is unstable and sensitive to electrical gain. Because the resonant sensor makes full use of the mechanical properties of silicon, it has very low hysteresis and repeatability errors and very good long-term stability. The repeatable temperature characteristics allow it to be corrected. The characteristics of these aspects together create the extremely high performance of the trench etching resonant pressure sensor under pressure and temperature changes.
Through the use of deep reactive ion etching technology, it can build any complex geometric structure in the resonant cavity. This is necessary to optimize the design and the performance of the resonator to achieve a higher pressure range and temperature range. In addition, the use of silicon fusion bonding allows the components of the sensor to be processed separately, and still retains the characteristics of single crystal silicon after being melted together. At the same time, the great flexibility of the sensor component design allows it to have a higher pressure and temperature range.
These two processes are accompanied by other proprietary design components, such as a new frequency detection method that obtains a stronger signal from the resonator, so that the sensor can be packaged with a heavy oil isolation diaphragm. Compared to other high-precision sensing technologies that are limited to dry, non-corrosive gases, this is a great improvement. In addition, the further development of related electronic devices in the trench-etched resonant pressure sensor makes it applicable to higher temperature environments.
Shinely High-speed Folding Box Glue mixed from much emulsions. This adhesives with special molecular structure can meet requirement of high speed producing and also can bonding various of materials.
63000PCS paper boxes will be ready in an hour.
Various of gluing, such as spraying, dish coating, roller coating, etc.
Easy resolution for materials gluing, such as PVC, PET, gold & silver card paper, BOPP film, PE coated paper, water ink, laser surface, polish surface, UV surface.
Application: Paper box for commodity, cosmetic, pharmaceutical, electronics etc.
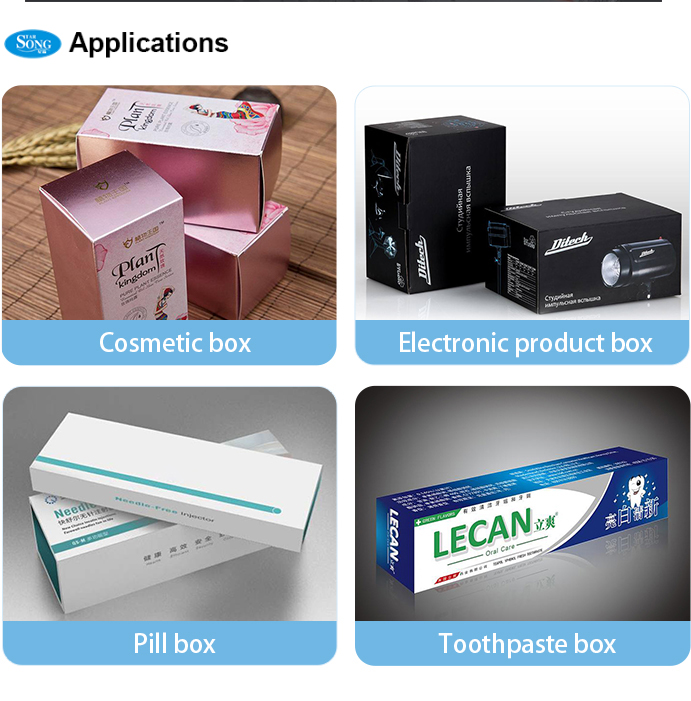

Application: Paper box for commodity, cosmetic, pharmaceutical, electronics etc.
Weatherability test:
Width 3.5cm strip from package sample and hang a 1kg hook. No tackless keep in -30℃~75℃ & humidity 85%RH for 7 days.
High-speed Folding Box Glue
Glue for Book Bonding,Book Binding Adhesives,glue paper to plastic bag,book binding glue spine
Guangdong Shinely New Materials Co., Ltd , https://www.shinelyglue.com